SEMI-e 第六届深圳国际半导体威廉希尔官方网站 暨应用展览会将持续关注产业核心威廉希尔官方网站 和发展前沿,向20多个应用领域提供一站式采购与威廉希尔官方网站 交流平台。
在SiC MOSFET 器件制备工艺中,多晶硅(Polysilicon)被广泛用于栅电极,多晶电极对关键线宽(CD)要求极高,业界趋向于采用较低的射频能量并能产生低压和高密度的等离子体来实现多晶硅的干法刻蚀。其中感应耦合等离子刻蚀威廉希尔官方网站 (ICP)得到大力应用。
随着功率器件尺寸的不断缩小,多晶硅栅的刻蚀越来越具有难度和挑战性。此外,作为栅电极的多晶硅需要通过掺杂磷元素的手段来实现更好的电导通特性,多晶原位掺杂对设备能力要求较高,当前业界仍多采用离子注入和退火推结的方式对多晶硅进行掺杂磷处理。掺磷扩散后的多晶硅表面完全不同于未掺杂多晶硅,这对干法刻蚀形貌提出了更高的要求。
为了保护 MOSFET 的栅极氧化层不被损伤,通常要把多晶硅刻蚀分成几个步骤:主刻蚀、着陆刻蚀和过刻蚀。主刻蚀通常有比较高的刻蚀速率,但是对氧化硅的选择比较小。通过主刻蚀可基本决定多晶硅的剖面轮廓和关键尺寸。着陆刻蚀通常对栅极氧化层有比较高的选择比以确保栅极氧化层不被损伤。一旦触及到栅极氧化层后就必须转成对氧化硅选择比更高的过刻蚀步骤以确保把残余的硅清除干净而不损伤到栅极氧化层。
刻蚀终点检测系统的原理如下,当发生侧面刻蚀时,可以借助于使刻蚀减少到最低量从而能控制线宽和边缘剖面到一定的程度。具体方法包括:
1) 刻蚀层的直接宏观检测;
2) 监测从刻蚀层的发射出的光波;
3) 用发射光谱法对等离子体刻蚀剂粒子的浓度检测;
4) 用发射光谱法或质谱法对刻蚀产物的检测;
5) 等离子体阻抗变化的检测。
终点检测对于刻蚀中工艺控制和工艺判断,都是一个有用的辅助手段,可以使材料组份和厚度的波动或工作参数的改变而引起的刻蚀速率的变化得到补偿。
多晶硅刻蚀原理(如图所示),F原子对 Si 的刻蚀是各向同性的,所以以 F原子为基础的化合物气体如 CF4、SF6等都不适宜用作多晶硅的刻蚀气体;而 Cl 原子对硅具有的各向异性刻蚀作用,所以 Cl2、HCl、SiCl4等气体都可以被采用。使用这些气体还有一个好处是,以 Cl 所形成的等离子体对 Si 及SiO2刻蚀的选择比较好,因此在多晶硅刻蚀结束后,可以使用同样性质的等离子体对聚酰亚胺(Polycide)进行过刻蚀,以确保多晶硅被刻净,而又不会刻蚀太多的 SiO2层。
平面型 SiCMOSFET 栅结构采用的多晶硅沟槽深度为 5000 A,属于浅沟槽刻蚀,其难点在于沟槽深度的均匀性控制,此外,为了满足沟槽隔离氧化物的填充要求,沟槽剖面轮廓的控制也非常重要,因为太垂直的轮廓不利于化学气相沉积(CVD)的沉积,通常会要求有适当的倾斜度。随着工艺尺寸的缩小,要求达到更高的深宽比使得剖面轮廓控制和深度均匀性控制受到更大的挑战。
当然 CD 的均匀性和剩余栅氧化层的均匀性也是重要的威廉希尔官方网站
指标。对于浅沟槽的刻蚀,Cl2和HBr 依然是主刻蚀气体,再配合小流量的氧气和氮气来产生氮氧化硅形成侧壁钝化层从而达到理想的刻蚀剖面轮廓,Ar 和He 通常用作辅助稀释的作用。
由于沟槽底部轮廓同样影响到氧化物的填充,采用 Cl2作为主刻蚀的气体容易形成比较直的剖面轮廓和凸型的底部轮廓,采用 HBr 作为主刻蚀气体能得到比较斜的剖面轮廓和凹形的底部轮廓。
审核编辑:刘清
-
多晶硅
+关注
关注
3文章
240浏览量
29281 -
MOSFET
+关注
关注
147文章
7159浏览量
213176 -
功率器件
+关注
关注
41文章
1762浏览量
90420 -
ICP
+关注
关注
0文章
70浏览量
12778
原文标题:多晶硅的刻蚀机理
文章出处:【微信号:Smart6500781,微信公众号:SEMIEXPO半导体】欢迎添加关注!文章转载请注明出处。
发布评论请先 登录
相关推荐
今日看点丨美国宣布提高中国太阳能硅片、多晶硅关税50%;联发科天玑 8400 芯片详细参数曝光
多晶硅栅工艺的制造流程
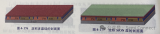
光伏多晶硅的应用领域有哪些
光伏多晶硅的分片方法及优缺点
多晶硅生产污水处理设备数据采集方案
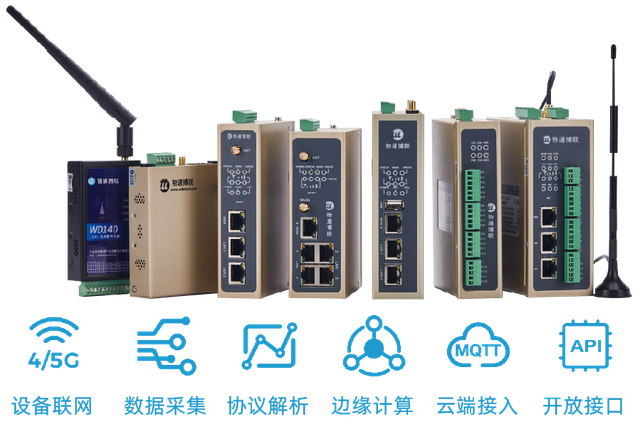
多晶硅栅耗尽效应简述

大全能源半导体级多晶硅项目首批产品出炉
大全能源半导体级多晶硅项目首批产品成功产出
控制多晶硅(poly-Si)/4H-SiC异质结二极管能垒高度(ΦB)的方法
浅谈安科瑞有源滤波器在多晶硅行业中的应用
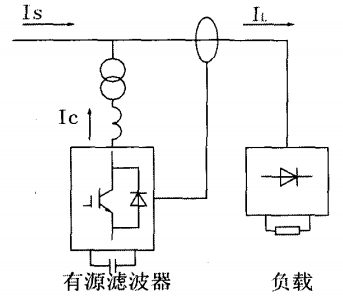
多晶硅的用途包括哪些
LPCVD和PECVD制备掺杂多晶硅层中的问题及解决方案
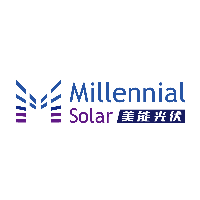
评论