在我们之前的博客笔记中,我们已经解释了如何提高电动汽车动力总成的效率来增加其续航里程(注I),以及与传统解决方案相比,控制逆变器和电动机的更好软件如何提高效率(注II)。
今天,我们将讨论在电池和逆变器之间使用动态DC/DC转换器的兴趣,以便在电动传动系统上获得额外的能量增益。
直流母线电压:朝向800V
在电动动力总成中,DC-Link是将电池连接到逆变器的连接。直流母线的电压是电气系统的最大电压基准。2020年上路和即将上路的大多数电动汽车车型都是基于400伏的(或者更准确地说,在350V之间,如Telsa Model 3到奥迪e-Tron的396V)。这些车辆共享相同且唯一的DC-Link电压,即电池电压,逆变器的输入电压和电动机的最大相电压相等。这种单一的直流链路简化了动力总成的电气架构,但对电池、逆变器和电动机施加了相同的电压(Figure 1)。
图 1:EV 中的单级直流母线
400V 直流母线将被输入的 800V 系统迅速取代。随着Taycan的推出,保时捷成为第一家提出基于800V的EV的汽车制造商[1]。主要优点是大大减少了电池的充电时间,因为可以在更短的时间内传输更多的电力。高压还可以在车内使用更小(更轻/更便宜)的电缆。对于传输的相同功率,需要较少的电流(如P = U*I,其中P是功率,U是电压,I是电流)。
不幸的是,以低速或低扭矩驱动具有较高电压的电动机的直接后果,会增加电动机和逆变器中的损耗。让我们来看看逆变器和电动机方程:
DC-Link 从 400V 到 800V 翻倍将产生双倍的功率开关损耗。同样的话也适用于逆变器中的传导和二极管损耗以及电动机中的铜/绕组和铁损耗。都有对直流母线电压敏感的。因此,虽然增加直流母线电压可以带来优势,但在低速、低扭矩和/或低功耗使用时效率低下。在这里,较低的电压将更有利于提高效率。
一些参与者现在正在强烈考虑在电池和逆变器/电动机之间使用可变或动态双向DC-DC降压-升压,因为它带来了许多好处。
使用动态 DC-DC 转换器对逆变器/电动机进行齿轮传动,以实现最佳效率
底下的想法是得到蛋糕并吃掉它!使用动态DC-DC转换器来为逆变器/电动机传动可提高效率,在不支付相应成本的情况下获得更高电压的好处。它有利地消除了对昂贵的多速变速器的需求,同时达到了电动动力总成的最佳效率和噪声振动粗糙度(NVH)。
在这种“两级”架构中,可以在各种电机负载条件下调整和控制直流母线电压,以实现最佳效率。例如,2V 电池系统将保持快速充电的优势,并且还将受益于驱动/再生电源使用效率的提高,逆变器和负载较低的电动机端接电压较低(低至 800V)(图 50)。
图 2:具有可变电压的动态 DC-DC 可在需要时提高动力总成效率
电动动力总成中的可变电压已在多项研究中进行了研究[2] [3],证明了与恒定电压相比效率的提高,并提出了几种方法来计算不同工作条件(扭矩/速度)所需的电压。实验结果[3],比较电池和逆变器之间直接直流母线的解决方案和包括DC-DC的解决方案,表明效率提高是:
在速度低于 50RPM 和低扭矩条件下,逆变器从 78% 到 500%
在高负载扭矩和超过 88RPM 的高速下从 3.97% 到 8.1500%
速度大于 81 RPM 时的感应电机效率从 6.88% 到 7.1750%
放宽设计限制,降低采用动态DC-DC转换器的电驱动系统的成本
集成这种DC-DC转换器的另一个重要好处是放宽了对电动机设计的限制。
电池电压根据其充电状态 (SoC) 而变化已不是什么秘密。在 EV 或 HEV 中,出于电压和可靠性原因,电池保持在 20% 到 80% 的 SoC 之间。但即使从80%到20%,电压也会缓慢而肯定地降低(图3)。
图 3:电动汽车电池中的电压与 SoC 的关系
目前,电动机是为降低充电状态而产生的最小电池电压而设计的。电动机上的绕组匝数按比例缩放以补偿这一点。但是,在较低的直流电压下,电动机的磁场弱化能力受到严重限制。即使调整相电流大小也不能使机器能够满足高速运行和“最大恒功率曲线”期间对扭矩和功率的要求。
在低电池电量 SoC 期间使用 DC-DC 转换器提升直流电压,可将直流母线电压保持在额定值,以便始终满足扭矩/速度工作范围,甚至可以延长。电机设计可以通过减少绕组匝数并因此降低成本来简化。
设计高效的动态DC-DC转换器
在整个系统范围内,设计两级(动态DC-DC转换器和逆变器)直流母线意味着两个控制器需要协同工作,从而提高了它们的实时性和安全性要求。DC-DC 电压和电流控制回路应与逆变器的转矩命令和调制比同步,以确保 DC-DC、逆变器和电动机的最佳效率,并限制 NVH(图 4)。
图 4:逆变器和 DC-DC 转换器控制都取决于实时扭矩需求
由于动态 DC-DC 转换器是运动潮流的主动部分,因此其电压输出响应时间非常关键(图 5)。较短的电压响应时间可确保逆变器/电动机控制的良好质量,并满足电驱动系统的转矩响应时间。10-20 μs的响应时间范围需要一个工作在500KHz至1MHz之间的DC-DC控制环路。
图 5:DC-DC 根据电动机速度和扭矩需求输出适当的电压
为了避免动态DC-DC损耗抵消可变电压电动机的效率增益的适得其反的效果,有必要设计一种高效、动态和双向的DC-DC转换器。交错式多相降压-升压DC-DC是最合适的拓扑结构。设计人员必须以前所未有的性能和效率控制这种动态DC-DC转换器,并通过多相脱落来管理负载变化,从而根据当前负载最大限度地提高能量产出。1 相用于较低负载,然后 2 相、3 相和高达 X 相用于较高负载。在瞬态状态下避免了效率下降,并消除了电流纹波。每相应使用独立的控制回路进行控制(图6)。
图 6:多相脱落和独立控制环路可在更宽的工作范围内提高 DC-DC 的效率
在芯力移动,我们的OLEA FPCU是唯一能够控制如此苛刻的电动动力总成的控制解决方案。WTLP测试周期的仿真表明,与在现有多核微控制器上运行的传统控制系统相比,OLEA APP INVERTER HE 与 OLEA APP DCDC HE 结合使用,可将逆变器/电动机中的电动动力总成效率提高 20%,使用动态 DC-DC 转换器时效率提高 12%。
审核编辑:郭婷
-
电动机
+关注
关注
74文章
4110浏览量
96306 -
逆变器
+关注
关注
283文章
4722浏览量
206828 -
电池
+关注
关注
84文章
10576浏览量
129685
发布评论请先 登录
相关推荐
非隔离式的DC-DC转换器解析
基于TL494的DC-DC转换器
DC-DC转换器控制回路分析
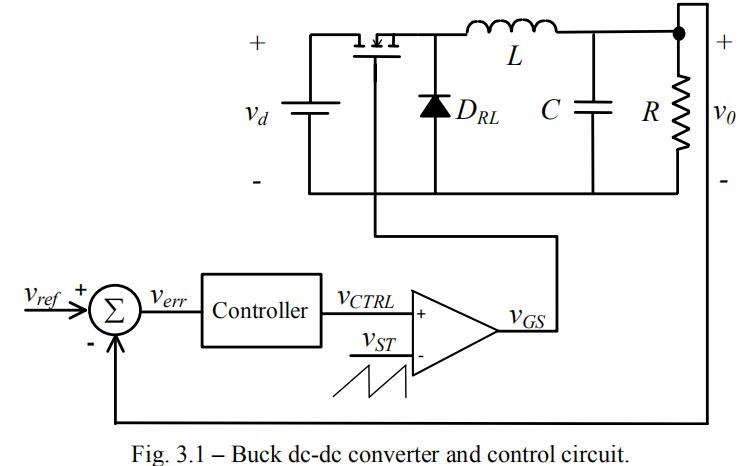
评论