PCB板翘,是让PCB设计工程师和PCB制造厂家都烦恼的难题。那么如何避免板翘,提高板子质量呢?
一、什么是PCB板翘?板翘的标准是?
板翘是行业的一个叫法,实际是指一张平整的PCB板发生了弯曲,也叫翘曲,严重点的翘曲有点像拱桥。
实际生产中,PCB不是100%平整的,多少有点弯曲。我们可以通过“翘曲度”来判断PCB的翘曲程度。
按照IPC标准,需贴片的PCB翘曲度需≦0.75%,才是合格产品。即PCB翘曲度超过0.75%,就判断为板翘,不合格。不需要贴片(只含有插件元器件) PCB 板,对其平整度要求低些,翘曲度放宽至≦1.5%即可。
实际上,为满足高精度和高速度贴装的需求,部分厂商对PCB翘曲度的要求更加严格,有要求翘曲度≦0.5%,甚至有个别要求≦0.3%。
翘曲度怎么计算呢?翘曲度=翘曲高度/曲边长度
根据这个计算公式,我们一般会用以下两种方法检测PCB翘曲度:
第一种方法是目前常见的检测方法——大理石检测法。它直接采用大理石测量,因为大理石相对会比较平整(或者使用厚度≧5mm的玻璃板也行)。具体的测量操作是将PCB平放在大理石上,四个角着地,测量PCB中间拱起的高度和PCB的对角线长度,再用拱起的高度除以PCB对角线长度,即得PCB翘曲度。
第二种方法是最先进测量方法——光学检测法,使用的设备是平面度测量仪。它利用光干涉原理来测量PCB翘曲度,精度可以达到0.1mil(2.54μm)。
二、PCB板翘的危害有哪些?
翘曲度过大,除了影响贴片外,还会影响SMT贴片机整机的可靠性。
对于不用贴片的PCB板,板翘会导致板上的插件元器件pin脚很难剪平整,PCBA板自然也无法装到相应的机箱或机内的插座上,导致不良影响整机的可靠性。因此,装配厂很烦遇到板翘的情况。
对于需要贴片的PCB板,板翘不仅会影响贴片质量,还可能会损坏SMT设备。在自动化SMT产线上,PCB板若不平整会引起难刷或刷不上锡膏的情况,还会引起定位不准,导致元器件无法贴装到焊盘上,甚至会撞坏自动插装机。
三、板翘是怎么造成的?8大常见原因
板翘的原因很多,总体来讲主要分两个大方面,一是制造商引起的,二是设计端引起的。
制造商引起的板翘原因会比较多,常见的有以下4种:
1.开料完后没做焗板,或者焗板时间不够。
2.V-CUT太深,导致两边V割的地方翘。
3.板材TG值太低,板子容易软化,导致无法接受高温引起板翘。
4.板厚低于1.0mm,出货前冷压板翘工艺不成熟,导致板翘。
工程设计端常见引起板翘的原因也有如下4种:
1.电路板上的铺铜面面积不均匀,一边多一边少。线路稀疏的地方相对于密集的地方,表面拉力会更薄弱,导致过高温的时候出现板翘。
2.可能由于介质特殊或者阻抗关系,叠层结构不对称,导致板翘。
3.板子本身镂空位置太大且很多,过高温的时候也容易板翘。
4.板子的拼板数量太多且拼板间距镂空,尤其是长方形的板子,也容易板翘。
四、避免板翘,PCB设计工程师应该这样做!
上干货!!
根据华秋客户的反馈,在设计端改善或避免板翘的常见方法有以下几种:
方法1:板内铺铜,增加板子表面的张力
当板子长度超过80mm以上,且板内没铺铜,同时板子偏薄(板厚低于1.0mm以下),这种会引起板翘。(这里讲的是FR4材料)
板子没铺铜前
编者建议是:在不影响功能的情况下,在板内铺铜,增加板子表面的张力,如果板内不能铺铜,又不能加板厚那只能采取压板翘。(资料是作者随意画的,仅供参考)
板子铺铜后
方法2:镂空区域铺铜并加工艺边,工艺边做铺铜
当板子有太多镂空位置,且板子过大时,过回流焊就会很容易弯曲。
镂空处没铺铜前
编者建议是:在镂空区域铺铜,减少板翘;另外板内在不影响功能的情况下,也做铺铜;最后建议是加工艺边,工艺边做铺铜。
镂空处铺铜后
方法3:芯板和PP片采用同品牌
多层板的芯板和PP片需要采用同品牌,不然会板翘。
比如6层板pp片不对称:2-3芯板的pp片薄,4-5的芯板pp片厚,这样压出来就会板翘。因此芯板和PP片都要用同品牌,保证厚度一样,保证多层板PP片对称。
五、翘曲PCB板的处理方法
由于各方原因,如设计不合理、防翘曲的工艺措施不落实等,最终PCB板就是出现了翘曲,该怎么办呢?
制造商可以将不合格的板子放到烘箱内,在150摄氏度及重压下烘 3~6 小时,并在重压下自然冷却;然后卸压把板子取出,再作平整度检查,这样可挽救部分板子。有的板子需作二到三次的烘压才能整平。若经过多次烘压,板子还是翘曲那就只能报废。
华秋电路是一家高可靠多层板制造商。1-32层PCB打样、中小批量生产、周期快、线上自助下单、平台跟踪订单进程。提供BOM配单,元器件采购,SMT贴片、PCBA一站式服务。欢迎咨询:https://www.hqpcb.com/?pcb_dzfsy
审核编辑黄昊宇
-
PCB设计
+关注
关注
394文章
4683浏览量
85555 -
PCB
+关注
关注
1文章
1795浏览量
13204
发布评论请先 登录
相关推荐
PCB板弯板翘的原因及改善措施
找到精通大功率PCB设计的工程师真的很难吗
深入剖析PCB翘曲现象:成因、危害与预防策略
如何有效避免PCB腐蚀过度
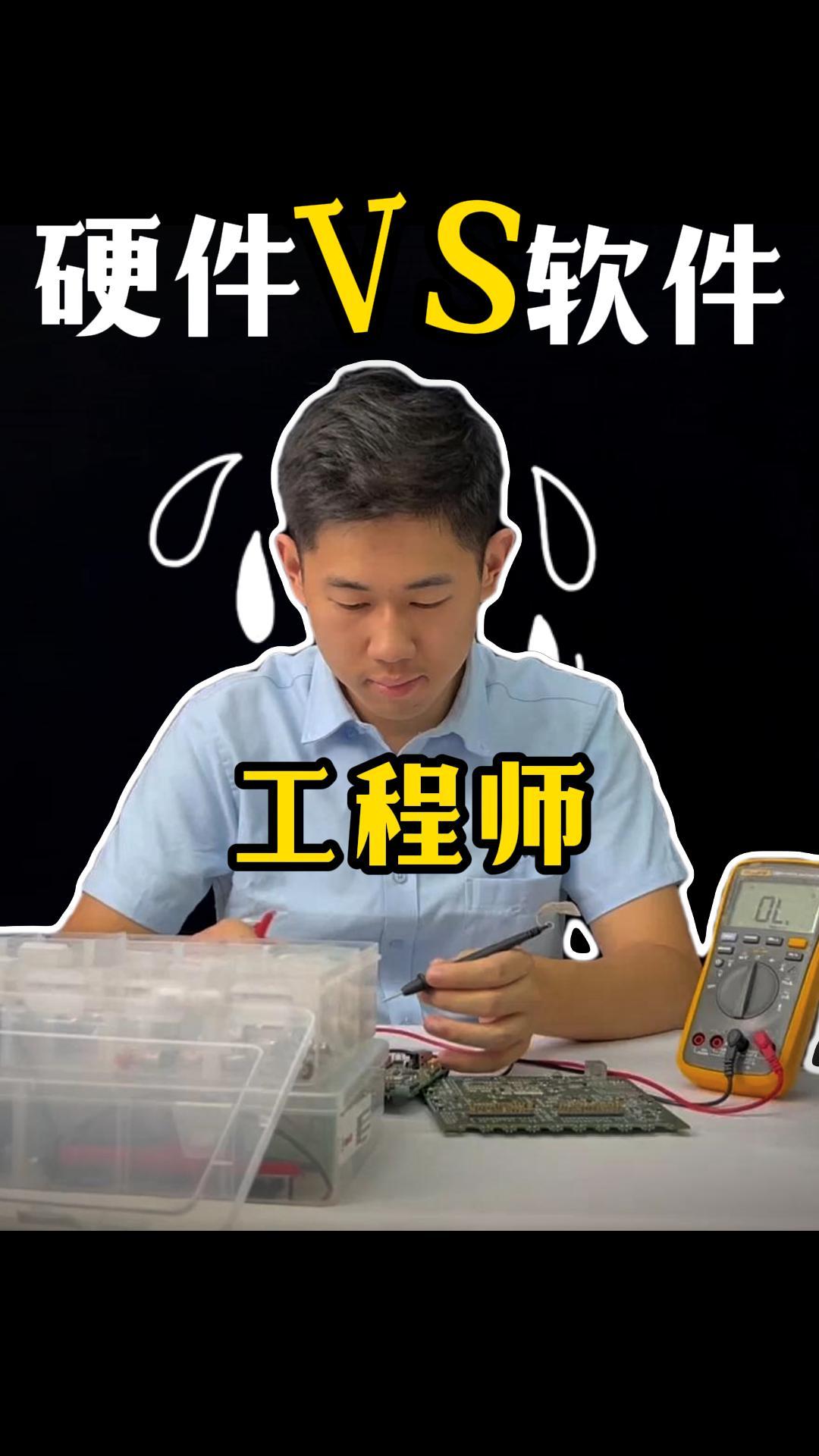
FPGA算法工程师、逻辑工程师、原型验证工程师有什么区别?
在树脂塞孔的设计上,工程师总觉得这样操作是节约成本其实是浪费
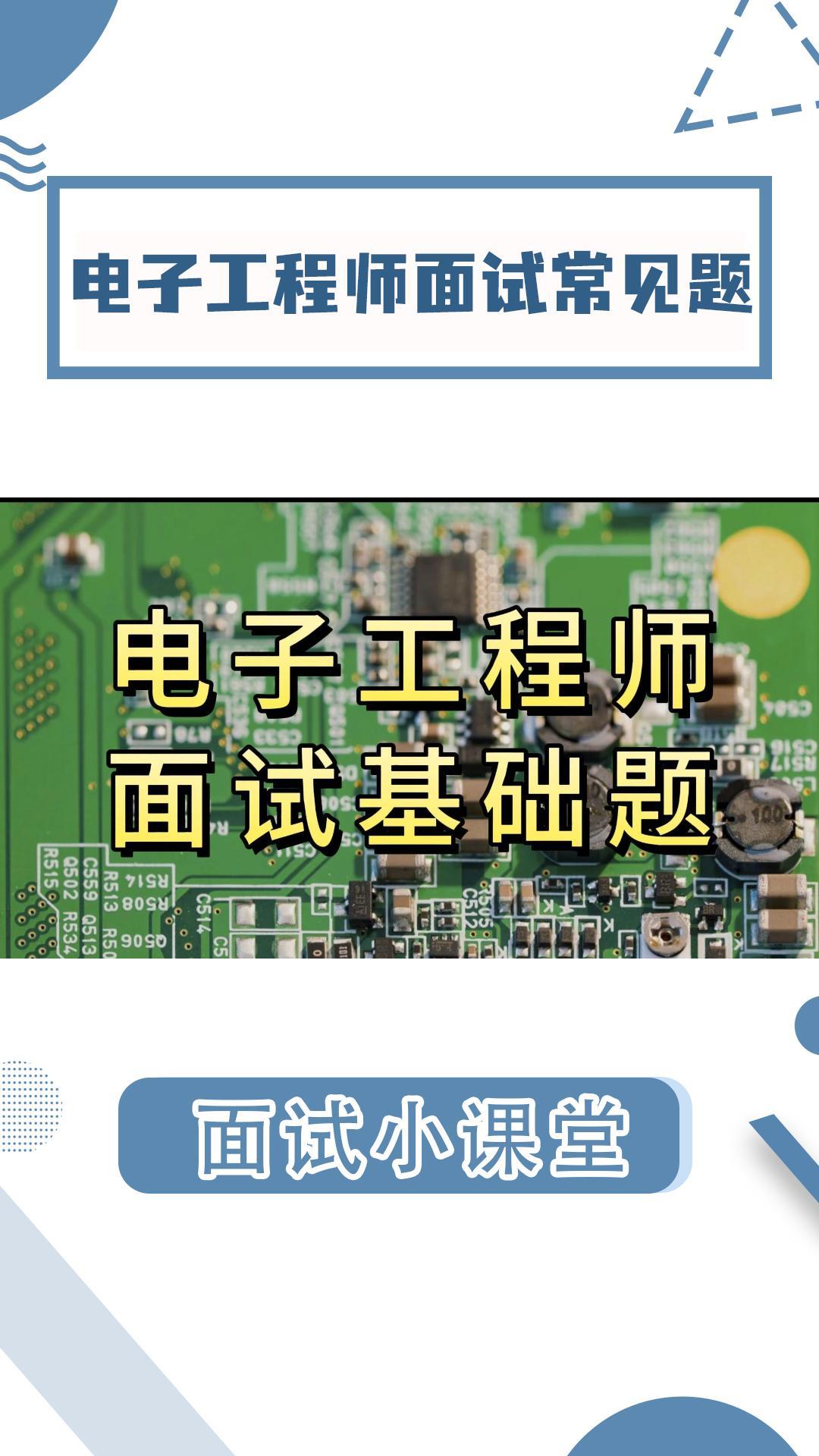
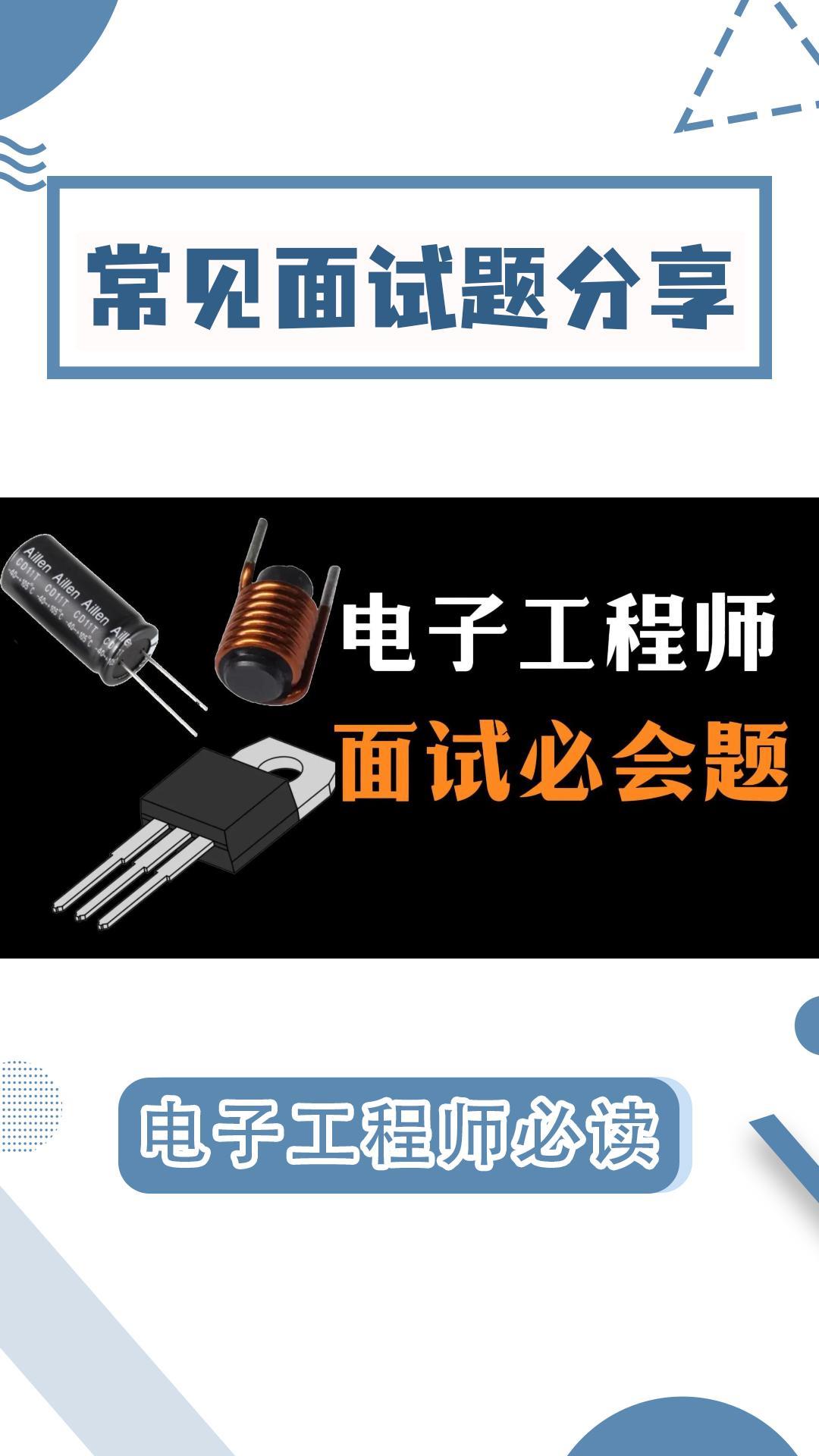
射频电缆组件选择和使用工程师指南
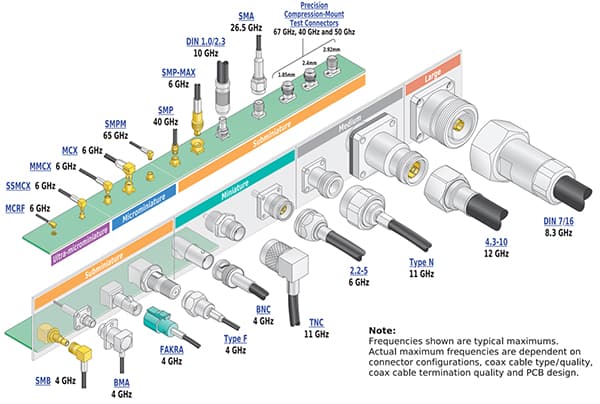
评论