齿轮是能互相吻合的有齿的机械零件,齿轮传动可完成减速、增速、变向等功能。它在机械传动及整个机械领域中应用极其广泛。今天对齿轮类零件的加工工艺做下归纳总结。
01、 齿轮的功用、结构
齿轮尽管由于它们在机器中的功用不同而设计成不同的形状和尺寸,但总可划分为齿圈和轮体两个部分。常见的圆柱齿轮有以下几类(下图):盘类齿轮、套类齿轮、内齿轮、轴类齿轮、扇形齿轮、齿条。其中盘类齿轮应用最广。
圆柱齿轮的结构形式
一个圆柱齿轮可以有一个或多个齿圈。普通的单齿圈齿轮工艺性好;而双联或三联齿轮的小齿圈往往会受到台肩的影响,限制了某些加工方法的使用,一般只能采用插齿。如果齿轮精度要求高,需要剃齿或磨齿时,通常将多齿圈齿轮做成单齿圈齿轮的组合结构。
02、 圆柱齿轮的精度要求
齿轮本身的制造精度,对整个机器的工作性能、承载能力及使用寿命都有很大影响。根据齿轮的使用条件,对齿轮传动提出以下几方面的要求:
1. 运动精度
要求齿轮能准确地传递运动,传动比恒定,即要求齿轮在一转中,转角误差不超过一定范围。
2.工作平稳性
要求齿轮传递运动平稳,冲击、振动和噪声要小。这就要求限制齿轮转动时瞬时速比的变化要小,也就是要限制短周期内的转角误差。
3. 接触精度
齿轮在传递动力时,为了不致因载荷分布不均匀使接触应力过大,引起齿面过早磨损,这就要求齿轮工作时齿面接触要均匀,并保证有一定的接触面积和符合要求的接触位置。
4. 齿侧间隙
要求齿轮传动时,非工作齿面间留有一定间隙,以储存润滑油,补偿因温度、弹性变形所引起的尺寸变化和加工、装配时的一些误差。
03、 齿轮的材料
齿轮应按照使用的工作条件选用合适的材料。齿轮材料的选择对齿轮的加工性能和使用寿命都有直接的影响。
一般齿轮选用中碳钢(如45钢)和低、中碳合金钢,如20Cr、40Cr、20CrMnTi等。要求较高的重要齿轮可选用38CrMoAlA氮化钢,非传力齿轮也可以用铸铁、夹布胶木或尼龙等材料。
04、齿轮的热处理
齿轮加工中根据不同的目的,安排两种热处理工序:
1. 毛坯热处理
在齿坯加工前后安排预先热处理正火或调质,其主要目的是消除锻造及粗加工引起的残余应力、改善材料的可切削性和提高综合力学性能。
2. 齿面热处理
齿形加工后,为提高齿面的硬度和耐磨性,常进行渗碳淬火、高频感应加热淬火、碳氮共渗和渗氮等热处理工序。
05、 齿轮毛坯
齿轮的毛坯形式主要有棒料、锻件和铸件。棒料用于小尺寸、结构简单且对强度要求低的齿轮。当齿轮要求强度高、耐磨和耐冲击时,多用锻件,直径大于400~600mm的齿轮,常用铸造毛坯。
为了减少机械加工量,对大尺寸、低精度齿轮,可以直接铸出轮齿;对于小尺寸、形状复杂的齿轮,可用精密铸造、压力铸造、精密锻造、粉末冶金、热轧和冷挤等新工艺制造出具有轮齿的齿坯,以提高劳动生产率、节约原材料。
06、齿坯的机械加工方案的选择
对于轴齿轮和套筒齿轮的齿坯,其加工过程和一般轴、套基本相似,现主要讨论盘类齿轮齿坯的加工过程。齿坯的加工工艺方案主要取决于齿轮的轮体结构和生产类型。
1. 大批大量生产的齿坯加工
大批大量加工中等尺寸齿坯时,多采用“钻一拉一多刀车”的工艺方案。 (1)以毛坯外圆及端面定位进行钻孔或扩孔。 (2)拉孔。
(3)以孔定位在多刀半自动车床上粗精车外圆、端面、切槽及倒角等。
这种工艺方案由于采用高效机床可以组成流水线或自动线,所以生产效率高。
2. 成批生产的齿坯加工
成批生产齿坯时,常采用“车一拉一车”的工艺方案
(1)以齿坯外圆或轮毅定位,精车外圆、端面和内孔。
(2)以端面支承拉孔(或花键孔)。
(3)以孔定位精车外圆及端面等。
这种方案可由卧式车床或转塔车床及拉床实现。它的特点是加工质量稳定,生产效率较高。
当齿坯孔有台阶或端面有槽时,可以充分利用转塔车床上的多刀来进行多工位加工,在转塔车床上一次完成齿坯的加工。
07、轮齿加工方法
齿轮齿圈的齿形加工是整个齿轮加工的核心。齿轮加工有许多工序,这些都是为齿形加工服务的,其目的在于最终获得符合精度要求的齿轮。
按照加工原理,齿形可分为成形法和展成法。成形法是用与被切齿轮齿槽形状相符的成形刀具切出齿面的方法,如铣齿、拉齿和成型磨齿等。
展成法是齿轮刀具与工件按齿轮副的啮合关系作展成运动切出齿面的方法,如滚齿、插齿、剃齿、磨齿和珩齿等。
齿形加工方案的选择,主要取决于齿轮的精度等级、结构形状、生产类型及生产条件,对于不同的精度等级的齿轮,常用的齿形加工方案如下:
(1)8级精度以下齿轮
调质齿轮用滚齿或插齿就能满足要求。对于淬硬齿轮可采用:滚(插)齿—齿端加工—淬火—校正孔的加工方案。但淬火前齿形加工精度应提高一级。
(2)6~7级精度齿轮
对于淬硬齿轮可采用:粗滚齿—精滚齿—齿端加工—精剃齿—表面淬火—校正基准—珩齿。
(3)5级精度以上齿轮
一般采用:粗滚齿—精滚齿—齿端加工—淬火—校正基准—粗磨齿—精磨齿。磨齿是目前齿形加工中精度最高,表面粗糙度值最小的加工方法,最高精度可达3~4级。
1. 铣齿
齿轮精度等级:9级以下
齿面粗糙度Ra:6.3~3.2μm
适用范围:单件修配生产中,加工低精度的外圆柱齿轮、齿条、锥齿轮、蜗轮
2.拉齿
齿轮精度等级:7级
齿面粗糙度Ra:1.6~0.4μm
适用范围:大批量生产7级内齿轮,外齿轮拉刀制造复杂,故少用
3.滚齿
齿轮精度等级:8~7级
齿面粗糙度Ra:3.2~1.6μm
适用范围:各种批量生产中,加工中等质量外圆柱齿轮及蜗轮
4. 插齿
齿轮精度等级:8~7级
齿面粗糙度Ra:1.6μm
适用范围:各种批量生产中,加工中等质量的内、外圆柱齿轮、多联齿轮及小型齿条
5. 滚(或插)齿—淬火—珩齿
齿轮精度等级:8~7级
齿面粗糙度Ra:0.8~0.4μm
适用范围:用于齿面淬火的齿轮
6. 滚齿—剃齿
齿轮精度等级:7~6级
齿面粗糙度Ra:0.8~0.4μm
适用范围:主要用于大批量生产
7. 滚齿—剃齿—淬火—珩齿
齿轮精度等级:7~6级
齿面粗糙度Ra:0.4~0.2μm
适用范围:主要用于大批量生产
8. 滚(插)齿—淬火—磨齿
齿轮精度等级:6~3级
齿面粗糙度Ra:0.4~0.2μm
适用范围:用于高精度齿轮的齿面加工,生产率低,成本高
9. 滚(插)齿—磨齿
齿轮精度等级:6~3级
齿面粗糙度Ra:0.4~0.2μm
适用范围:用于高精度齿轮的齿面加工,生产率低,成本高
08、齿端的加工
齿轮的齿端加工有倒圆、倒尖、倒棱和去毛刺等方式,下图所示。倒圆、倒尖后的齿轮在换档时容易进人啮合状态,减少撞击现象。倒棱可除去齿端尖边和毛刺。
a)倒圆 b)倒尖 c)倒棱
齿端加工
下图是用指状铣刀对齿端进行倒圆的加工示意图。倒圆时,铣刀高速旋转,并沿圆弧作摆动,加工完一个齿后,工件退离铣刀,经分度再快速向铣刀靠近加工下一个齿的齿端。齿端加工必须在齿轮淬火之前进行,通常都在滚(插)齿之后,剃齿之前安排齿端加工。
齿端倒圆
09、直齿圆柱齿轮加工工艺过程
高精度齿轮
1.毛坯锻造
2. 正火热处理
3. 粗车外形、各处留加工余量2mm
定位基准:外圆和端面
4.精车各处,内孔至Φ84.8H7,总长留磨削余量0.2mm,其余至尺寸
定位基准:外圆和端面
5. 检验
6. 滚切齿面,留磨齿余量0.25~0.3mm
定位基准:内孔和端面A
7. 倒角
定位基准:内孔和端面A
8. 钳工去毛刺
9. 齿面高频淬火HRC52
10. 插键槽
定位基准:内孔和端面A
11. 靠磨大端面A
定位基准:内孔
12. 磨削B面至总长
定位基准:端面A
13. 磨内孔至φ85H5
定位基准:内孔和端面A
14. 齿面磨削
定位基准:内孔和端面A
15. 检验
10、齿轮加工工艺过程分析
1. 定位基准的选择
对于齿轮定位基准的选择常因齿轮的结构形状不同,而有所差异。带轴齿轮主要采用顶尖定位,孔径大时则采用锥堵。顶尖定位的精度高,且能做到基准统一。带孔齿轮在加工齿面时常采用以下两种定位、夹紧方式。
(1)采用面向定位端面的夹紧方式。这种方式可使定位基准、设计基准、装配基准和测量基准重合,定位精度高,适于批量生产。但对夹具的制造精度要求较高。
(2)以外圆和端面定位工件和夹具心轴的配合间隙较大,用千分表校正外圆以决定中心的位置,并以端面定位;从另一端面施以夹紧。这种方式因每个工件都要校正,故生产效率低;它对齿坯的内、外圆同轴度要求高,而对夹具精度要求不高,故适于单件、小批量生产。
2. 齿轮毛坯的加工
齿面加工前的齿轮毛坯加工,在整个齿轮加工工艺过程中占有很重要的地位,因为齿面加工和检测所用的基准必须在此阶段加工出来;无论从提高生产率,还是从保证齿轮的加工质量,都必须重视齿轮毛坯的加工。
在齿轮的威廉希尔官方网站 要求中,应注意齿顶圆的尺寸精度要求,因为齿厚的检测是以齿顶圆为测量基准的,齿顶圆精度太低,必然使所测量出的齿厚值无法正确反映齿侧间隙的大小。
所以,在这一加工过程中应注意下列三个问题:
(1)当以齿顶圆直径作为测量基准时,应严格控制齿顶圆的尺寸精度
(2)保证定位端面和定位孔或外圆相互的垂直度
(3)提高齿轮内孔的制造精度,减小与夹具心轴的配合间隙
审核编辑:郭婷
-
机器
+关注
关注
0文章
781浏览量
40723 -
测量
+关注
关注
10文章
4857浏览量
111269
原文标题:一文搞懂齿轮类零件的那些加工工艺!
文章出处:【微信号:AMTBBS,微信公众号:世界先进制造威廉希尔官方网站 论坛】欢迎添加关注!文章转载请注明出处。
发布评论请先 登录
相关推荐
自动零件分析仪的原理和应用
数控机床加工工艺方法分类有哪几种
数控铣床主要用于加工什么零件
数控加工工艺处理的原则和步骤是什么
数控加工工艺主要包括哪些内容和特点
简述数控机床的加工过程与组成
特斯拉拟将零件生产线移出中国
千万不要忽视了零件选型调用
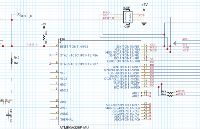
SMT贴片电阻电容小零件发生空焊及立碑效应的原因?如何改善呢?
面向智能制造的机加工艺管理流程
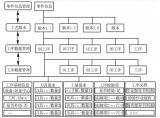
高精度微型加工中心——半导体精密零件加工的新选择
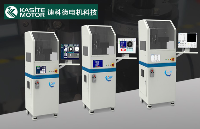
评论