01
快速加热氧化(RTO)
随着晶体管关键尺寸的缩小,栅氧化层的厚度也变得很薄。最薄的栅氧化层只有15A,而且由于栅漏电流越来越大,这个厚度已经不能再减小。当这样薄的栅氧化层使用多晶圆批量系统如氧化炉时,很难精确控制氧化层的厚度和晶圆对晶圆的均匀性。使用单晶圆RTP系统生长高质量超薄氧化层有许多优点,由于RTP系统能精确控制整片晶圆的温度均匀性,因此快速加热 氧化(RTO)系统能生长薄且均匀的氧化层。对于单晶圆系统,RTO过程的晶圆对晶圆均匀性控制比高温炉工艺好,尤其对于超薄氧化层;另一个优点是RTO反应室的主机平台可以和氟化氢蒸气刻蚀反应器整合在一起。当氟化氢蒸气刻蚀移除了硅晶圆表面的原生氧化层后,就可以将晶 圆经过高真空转移室送入RTO/RTA反应室。由于晶圆不会暴露在大气和湿气中,因此硅表面就不再有氧化的可能性,接着就可以将晶圆送到RTO反应室进行HC1清洗、氧化和退火处理。
下图为RTO工艺的流程图。将晶圆载入反应室后就可以打开加热灯管分两步提升温 度:首先以较大的升温速率将温度升高到800摄氏度左右,接着再以较低的速率获得所需的氧化温度,如1150摄氏度这种两步升温的过程可以缩短升高温度所需的时间,因为第二步使用较低的速率升温达到氧化工艺所需的温度可以缩短稳定温度所需的时间。当温度稳定后,将氧气注入反应室使氧和硅反应后在硅晶圆表面生成二氧化硅。无水性氯化氢也可以用在氧化过程中减少移动离子的污染和降低界面电荷。氧化层生成之后便将O2和HC1气流关闭并注入氮气, 然后将晶圆温度升高到1100摄氏度左右对氧化层进行退火,这个过程可以改善氧化薄膜的质量并进一步降低界面电荷。包含一氧化氮(NO)的热氮化可以在此退火过程中形成。如果需要等离子氮化,晶圆需要被送到另一个反应室,然后经过退火工艺。退火过程结束后就将加热灯管关掉,晶圆开始冷却,转移室内的机器手会将炽热的晶圆送到冷却室,最后再将晶圆放入晶圆盒内。栅介质已经开始从常用的二氧化硅发展为硅氧氮化合物(SiON),最后发展使用具有高介电常数的介质层,从而使得可以使用较厚的栅极介电层以防止栅极漏电流和栅电介质击穿。原子层沉积(ALD)方法常用于形成高电介质,RTA热处理工艺用来提高薄膜的质量,并减少界面态电荷。
由于RTO热处理具有更好的工艺控制,尤其是晶圆到晶圆的均匀性控制,所以已被广泛 用于栅氧化工艺。除湿式氧化外,最先进的集成电路芯片的氧化过程都在RTO工艺室内进 行,这是由于其具有更好的热积存控制。
02
快速加热CVD
RTCVD过程是在一个单晶圆、冷壁式的反应室中进行的加热CVD工艺,具有快速改变温 度并精确控制温度的能力(见下图)。由于是单晶圆系统,所以必须有足够高的沉积速率使 薄膜沉积过程在1 ~2 min内完成,这样才能达到每小时生产30〜60片晶圆的生产能力。
下图显示了快速加热化学气相沉积(RTCVD)过程和低压化学气相沉积(LPCVD)时的温度变化。与高温炉LPCVD过程比较,RTCVD过程在热积存和晶圆对晶圆的均匀性上有好的控制能力。由于元器件尺寸不断缩小,前段工艺所形成的沉积薄膜厚度也随之减小,一般在 100 - 2000 A之间。随着沉积速率从100 A/min到1000 A/min,单晶圆RTCVD工艺在前段的薄膜沉积中很受欢迎。
审核编辑 :李倩
-
集成电路
+关注
关注
5388文章
11547浏览量
361840 -
电流
+关注
关注
40文章
6863浏览量
132198 -
RTO
+关注
关注
0文章
16浏览量
11179
原文标题:半导体行业(一百三十七)——加热工艺(十八)
文章出处:【微信号:FindRF,微信公众号:FindRF】欢迎添加关注!文章转载请注明出处。
发布评论请先 登录
相关推荐
MOSFET晶体管的工艺制造流程
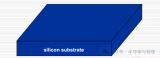
SMT工艺流程详解
源代码解析工具与自动化流程图生成解决方案
简述连接器的工艺流程
系统集成部署流程图
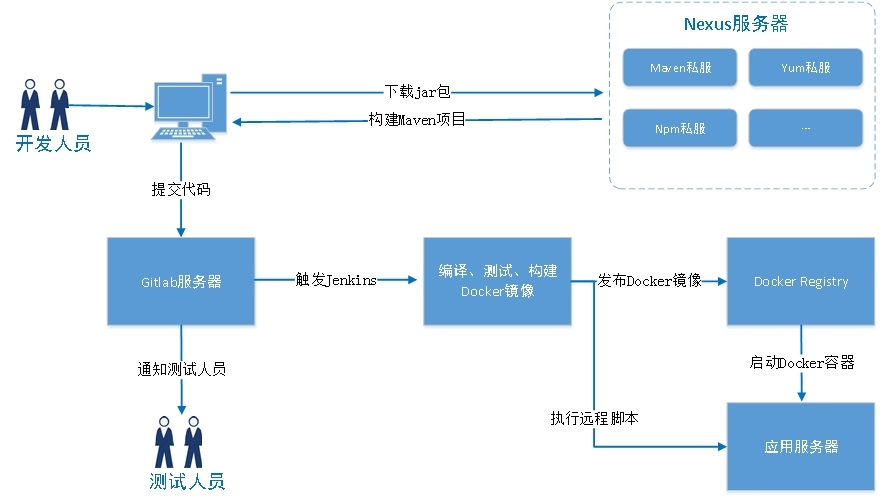
评论