摘要:从螺栓啮合表面摩擦系数变化入手,研究了振动状态下螺栓的松动行为,根据振动试验结果把螺栓松动过 程分为了四个阶段。结合螺纹的有限元受力分析及扫描电镜磨损图像,在理论与微观两方面对螺纹接触压力、接触 剪力和相互滑动区域的分布进行分析,对压力和滑动导致的表面磨损而引起的摩擦系数变化进行了分析,研究引起 摩擦系数变化的微观原因,得出摩擦因数是引起松动阶段性变化的主要原因。
0 引言
螺栓连接结构广泛应用于飞机、汽车、各种机械及结构中,是各种机械设备和结构件中最基本的连接方式。由振动引起的螺栓松动现象,是螺栓失效的主要形式。做振动状态下螺栓松动原因的研究主要有Pai 和Hess[1 - 2], Izumi[3]及Koch[4],他们认为是螺纹及螺帽的滑动导致了螺栓的松动。Jiang 等人[5 - 6]研究了螺纹根部塑性变形导致的螺栓松动。摩擦力是螺栓保持拧紧状态的关键因素,摩擦力影响着螺纹啮合面及螺帽承力面的拧紧力矩,进而影响拧紧力矩产生的轴向应变引起的预紧力,当把螺帽拧紧到螺栓上时,是摩擦力的作用阻止螺母旋转松脱。虽然摩擦力是螺栓防松的基本因素,但是在振动状态下连接件的螺栓摩擦力变化还没有确切的研究。所以以共振状态下的螺栓预紧力松弛试验来研究螺栓松动过程,结合螺纹啮合面的扫描电镜形貌图分析了摩擦系数对松动过程的影响并对摩擦系数变化的微观原因进行了分析。
1 振动松弛实验
试验所用的试验件是两块上下叠加的45 号钢矩形板条,厚度分别为8 mm、3 mm,连接板试验件通过单排螺栓连接构成( 图1) ,螺栓为普通M5 螺栓。
振动试验系统( 图2) 主要包括激励系统、控制系统和采集系统。激励系统设备主要是振动台; 控制系统设备包括振动台控制系统,功率放大器; 采集系统设备包括动态应变采集仪、电阻应变计和压电式加速度传感器。用夹具将试验连接板的一端固定在振动台上,另一端加配重块。实验分为正弦扫频与正弦定频实验。扫频试验频率范围为5 Hz ~ 500 Hz,扫频持续时间为3 min。扫频试验主要目的是测出螺栓连接结构件的共振频率,然后
用该固有频率对螺栓连接结构件进行正弦定频振动,正弦定频试验测量数据为螺栓的轴向力。正弦振动的位移设为3 mm,频率为共振频率,在实验过程中每隔10 min 停机一次,对数据进行整理、存储,检查试验件是否发生破坏,对预紧力变化数据整理存储。
设计测力传感器测量螺栓的轴向力,测力传感器由空心圆筒和电阻应变片组成,空心圆筒的高度和厚度根据圣维南原理设计,测力传感器所用材料为45#钢。用密封胶来密封电阻应变片进行防护,保证电阻应变片的绝缘电阻以及振动测试时电阻应变片不受到损害。最后将电阻应变片接入动态应变采集仪上,检查测试通道,对动态应变采集仪进行平衡与清零操作,确保采集数据没有零点漂移现象。
测力传感器安装在螺母与连接板之间,通过测力传感器即可得到螺栓的轴向预紧力,进而达到检测螺栓预紧力的目的,测力传感器安装如图3 所示。考虑到传感器承受轴向的压力,可能会出现偏载产生弯矩,同时螺母与传感器接触面在旋进的过程中也会产生一定的扭矩,全桥测试法具有桥臂系数大,且可以消除由于载荷偏心产生的附加弯矩对测量值的影响,本实验用全桥测试法对螺栓预紧力进行测量,并根据测量出的螺栓预紧力值调整预紧程序。
2 实验结果及分析
2. 1 预紧力变化
动态应变仪采集到螺栓的轴向力变化,可以看出螺栓预紧力在振动状态下的松弛过程。图4 中横坐标代表时间,纵坐标代表预紧力。试验施加的预紧应力范围σp = ( 0. 5 ~ 0. 6) σs,保证其在弹性变形阶段,在位移振动激励下,螺栓预紧力初始基本保持不变,30 min 后开始缓慢下降,表明螺栓出现了松动,120 min 后快速下降,曲线斜率明显变大,150 min 后曲线变化平缓,预紧力基本上不再变化,螺栓已经松弛失效。与以往的试验结果[7]相比,预紧力并不是从一开始就下降,而是经历了一段平稳变化的过程,这是由于位移载荷与力载荷作用下预紧力变化的不同,而该阶段的不同主要是由于摩擦系数的变化不同造成的。
在振动载荷作用下,把螺栓预紧力的变化经历分为四个阶段。
第一阶段由于摩擦系数的增大,螺纹的螺旋形结构产生了松弛力矩,外载荷作用下接触面间的剪切力产生的松弛力矩与摩擦力矩是相平衡的,螺栓没有松动。该阶段在以往的螺栓预紧力松弛分析研究中没有出现,因为本实验是对连接结构件整体采用位移加载振动,而不是激振力振动,引起螺栓松动的剪切力由连接板的挤压变形提供,该剪切力变化复杂且幅值较小。
第二阶段由于摩擦系数的减小,摩擦力矩不足以克服松弛力矩,螺栓开始松动,轴向的应变减小,螺栓的预紧力出现小幅下降。
第三阶段螺纹副无法满足自锁条件而使螺母回转,螺栓轴向应变快速减小,预紧力也急剧下降。
第四阶段螺栓已经松弛失效,预紧力达到最小值。螺栓需要进行拧紧,否则会影响连接件的刚度及紧密度,造成连接件分离,发生故障。
2. 2 螺纹啮合面微观分析
从图5 中可以看到螺纹斜面在反复碾磨下产生磨屑碎片与划痕,表面不光滑,这些区域越接近齿尖位置,磨损越严重。接触滑动产生的变形过程会产生滑移带,滑移带的移动可能与杂质相交,生成更多的位错,位错堆积的地方会形成微观裂纹[8],这些对摩擦系数都有一定的影响。
第一阶段预紧力没有变化,螺纹在接触力作用下发生扭曲变形,尤其以齿尖处的接触压力最大,变形会使表面轻微磨损[9],这些螺纹接触面的磨损破坏导致了接触表面摩擦因数的增大。
第二阶段在接触压力及滑动作用下螺纹表面发生塑性变形,塑性变形不断地积累使得亚表面位错密度不断增加,发生了位错堆积,当位错与一些缺陷相遇时,便会形成空穴,随着滑动的继续,局部的地方会发生剧烈的冷却硬化现象,材料就会变得很脆,接触表面的滑动过程中会产生磨屑颗粒,通常称为第三体,由图6 中可以看到,划痕带表面产生了许多裂纹,这些微裂纹相互挤压、碎化并且渐渐贯通,表面就会呈颗粒状脱落,磨屑的作用是它作为磨料加速表面损伤,又可以分开两表面减少接触,第三体的出现引起摩擦力系数的下降。
第三阶段滑动产生了大量的磨屑并截留在螺纹表面之间,表面材料与磨屑相互摩擦,磨屑对粗糙的表面“抛光”,接触表面变得光滑( 图7) ,使得螺栓摩擦系数降低。
第四阶段摩擦因数降到最小值并保持不变。
综合以上分析,摩擦系数经历了先增大,后缓慢减小,又快速减小直到降到最低值的过程,摩擦因数的变化与松动过程紧密联系,控制摩擦因数的变化对于螺栓的防松设计有重要影响,在拧紧过程中使用润滑油非常有必要,以减少接触表面的滑动磨损。摩擦系数的不同变化是由于表面磨损情况决定的,以螺栓连接件建立有限元分析模型,对螺纹处的磨损原因进行分析,进而研究摩擦系数变化。
2. 3 啮合表面有限元计算
通过有限元分析软件得到螺纹表面的接触压力与剪切力。螺栓接触面的滑动与接触面的法向应力的分布与切向应力的分布有关,法向应力影响摩擦力,切向应力影响滑动。螺纹的牙型角是60°,螺纹斜面上牙型角方向的法向应力σ1与切应力τ1沿着螺纹斜面分布。螺纹的升角是3. 25°,螺旋升角方向斜面的法向应力为σ2,切应力为τ2。在螺纹的齿尖位置,受到较大的压力与剪切力作用,压力导致齿尖位置出现塑性变形,剪切力引起相互滑动,在塑性变形与滑动作用下,齿尖位置出现严重磨损迹象。从扫描电镜图像( 图5) 也可以看到有明显的磨损及裂纹,磨损情况的不同导致了摩擦系数变化不同。
图10 中的曲线代表某一螺纹的根部、中部及齿尖处的横向滑动位移,在4 ~ 6 s内施加了预紧力,在7 ~ 10 s 内加载了3 mm 的位移载荷。可以看出螺纹表面的滑动主要发生在螺纹面的齿尖位置与中部,而螺纹根部由于发生了弹性变形而导致其横向滑动位移没有其它两处的值大。这也解释了扫描电镜观察下的螺纹形貌图中,螺纹表面的中部与齿尖有明显的滑动磨损( 图6) 。在压力及滑动作用下,齿尖位置受损严重,产生了大量的磨屑颗粒,螺纹中部的疲劳裂纹萌生并扩展,这些因素均导致了摩擦系数的下降。
3 结论
本文研究了共振状态下螺栓的松动行为,结论如下:
1) 位移振动下的初始阶段,螺栓预紧力没有直接下降,而是经历了一段平稳变化的过程,这段过程是由于摩擦系数的增大而没有发生松弛。
2) 基于有限元分析结果对螺纹接触表面的接触力分布及相对滑动分析,结合螺纹的扫描电镜形貌图,发现齿尖位置受到压力最大; 中部及齿尖位置的滑动现象比较明显,压力下的变形及滑动导致这两处的表面磨损加剧。
3) 磨损程度的不同而引起的摩擦因数的不同变化把松动过程分为了四个不同的阶段。第一阶段,轻微的磨损破坏使得表面摩擦因数增大; 第二阶段,微裂纹贯通导致材料脱落而磨屑产生,磨屑引起摩擦因数的下降; 第三阶段,接触表面截留大量的磨屑,而磨屑对粗糙表面有“抛光”作用,接触表面变得光滑,因而摩擦因数快速下降。第四阶段,摩擦因数降到最低值,螺栓已完全松动。
-
控制系统
+关注
关注
41文章
6611浏览量
110588 -
螺栓
+关注
关注
0文章
63浏览量
9500 -
扫描电镜
+关注
关注
0文章
77浏览量
8991
原文标题:振动状态下螺栓松动行为及原因分析...
文章出处:【微信号:线束专家,微信公众号:线束专家】欢迎添加关注!文章转载请注明出处。
发布评论请先 登录
相关推荐
五款电源运行Furmark状态下的不同功耗
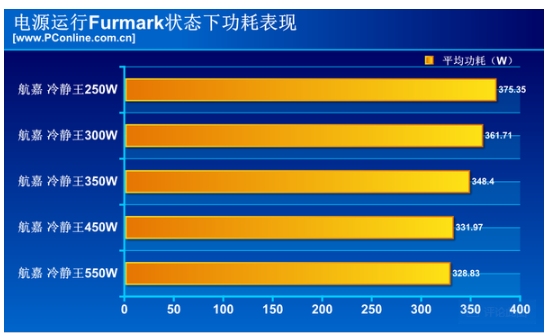
电缆故障的主要原因
精确诊断风机机组地脚螺栓松动故障
MOS管工作在开关状态下的Miller效应的原因与现象分析
螺栓经常松动严重影响生产?
螺栓松动原因分析
如何在connected idle状态下向手机同步音量
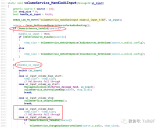
评论